Sys2PEP - Systemmodelle als Werkzeug des digitalen Produktentstehungsprozesses
Ein durch das Zentrale Innovationsprogramm Mittelstand des Bundesministeriums für Wirtschaft und Energie gefördertes Forschungsprojekt. Durchgeführt von der B&W Software GmbH, dem Institut für Produkt Engineering der Universität Duisburg-Essen (IPE) und der SMS group GmbH.
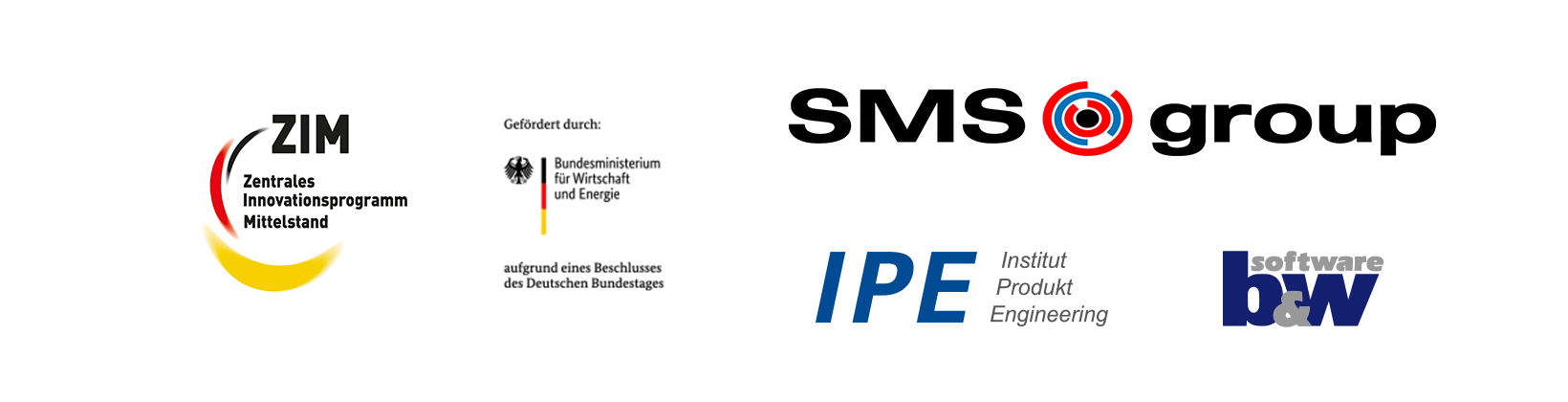
Problem
Produktfamilien mit verschiedenen Varianten in ihren Wirkprinzipien und Ausgestaltungen erweisen sich in ihrem Entstehungsprozess oftmals als komplex. Daraus resultiert ein hoher Zeitaufwand in Konstruktion und Auslegung. Da solche Aufträge oftmals von denselben Anwendern durchgeführt werden, entsteht zudem eine zentrale Wissensanhäufung bei einer geringen Personengruppe. Um den Prozess vom Kundenauftrag zum fertigen Produkt effizient und zugänglich zu gestalten, ist eine systemtechnische Unterstützung unausweichlich.
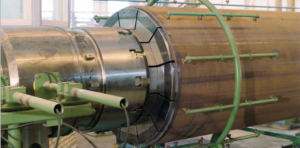
Lösungsansatz
Die Produktfamilie wird mittels einer formalen Beschreibungssprache in eine Referenzarchitektur übertragen. Hierbei werden mehrere Elemente modelliert und durch Abhängigkeiten, Attribute und wichtige Parameter beschrieben.
Ausgehend von definierten Berechnungs- und Gestaltungsvorschriften werden daraus verschiedene Konfigurationen des Produktes erzeugt. Abschließend werden diese in ein 3D-Modell überführt.
Durchführung
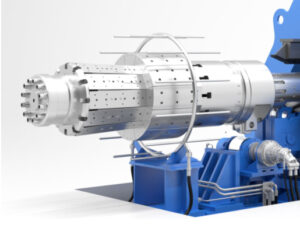
Zur Erzeugung dieses Prozesses zogen wir die Produktfamilie der Expanderwerkzeuge der SMS group heran. Diese besitzt eine hohe Variation in ihrer Gestaltung in Abhängigkeit der Kundenanforderungen. Angesichts dessen eignete sich dieses Werkzeug für dieses Projekt.
Mit Hilfe eines Reverse-Engineering Ansatz war es möglich das Produkt bis auf seine funktionale Architektur in einem Top-Down Prozess zu analysieren. Das Identifizieren der logischen Zusammenhänge zwischen den Strukturelementen erfolgte im stetigen Wissenstransfer zwischen den Projektpartnern.
Die IPE beschrieb die Referenzproduktarchitektur mittels der Systemmodellierungssprache SysML. Diese ist basierend auf UML 2(Unified Modeling Language) und findet ihren Einsatz beim Beschreiben von komplexen Systemen.
Die Model-Based-Systems-Engineering (MBSE) Umgebung „Cameo Systems Modeler“ stellte Zusammenhänge der Produktfamilie grafisch dar. Als Ergebnis lieferte sie die geometrischen Ausprägungen einer Produktkonfiguration in Form von Parametern. Das von uns entwickelte SmartAssembly übertrug die Resultate zwischen MBSE- und CAD-System. Dadurch erhielten wir ein hohes Maß an Flexibilität, welches ein schnelles Reagieren auf die wechselnden Anforderungen des Produktentstehungsprozesses erlaubt. Die Schnittstelle zwischen den beiden Systemen hat dabei eine XML-Struktur gebildet.
Die Aufgaben auf Seiten des CAD-Systems bestanden darin die XML-Daten in ein 3D-Modell zu übertragen und sicherheitskritische Features auszulegen. Dafür schufen wir verschiedene Analysemodelle und hinterlegten in diesen Entscheidungsmechanismen. Anhand dieser war es möglich sicherheitskritische Elemente zu überprüfen und daraus eine Gestaltung für einige Komponenten festzulegen. Dies erwies sich als äußerst hilfreich, da für die Beschreibung einiger geometrischer Ausprägungen die Möglichkeiten im Systemmodellierer einen nicht zu rechtfertigenden Mehraufwand bedeutet hätten. Zudem erzeugten wir im CAD-System eine Struktur, welche die Platzierung der Komponenten in Abhängigkeit der Kundenanforderung steuerte. Dabei modellierten wir das Werkzeug bereits in seiner groben Struktur als Skelett. Anschließend passten wir dieses mit SmartAssembly an Variante und Berechnungen an.
Fazit
Durch den Einsatz einer formalen Beschreibungssprache war es möglich, die physische Struktur der Produktfamilie mit all ihren Abhängigkeiten in eine digitale Referenzstruktur zu überführen. Daraus resultierte eine schnelle und reproduzierbare Auslegung des fertigen Produktes unter Berücksichtigung der Kundenanforderungen. Zudem gelang es uns durch den Einsatz von SmartAssembly, äußerst flexibel auf die variablen Anforderungen zwischen MBSE- und CAD-Umgebung zu reagieren. Gleichzeitig konnten wir die Berechnungsergebnisse in ein CAD-Modell überführen. Die Kombination aus den Stärken der beiden Systeme ermöglichte es selbst komplexe und sicherheitskritische Features auszulegen und zu validieren.
Aufgrund dieses Forschungsprojektes ist durch die Zusammenarbeit aller Projektpartner ein neuer Produktentstehungsprozess entstanden. Dadurch wird es möglich, das bestehende Know-how einer Produktfamilie in eine digitale Struktur zu extrahieren und diese in ein 3D-Modell zu überführen.
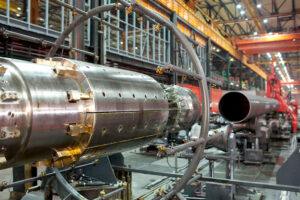