Optimization of the design process: Traceable library components in Windchill
The stated objective of our client was to find a process that enables the creation of a library for components and geometries via PDM-Link (Windchill), allowing for tracking of their usage within the company. Additionally, the aim is to achieve a more efficient workflow for the designer.
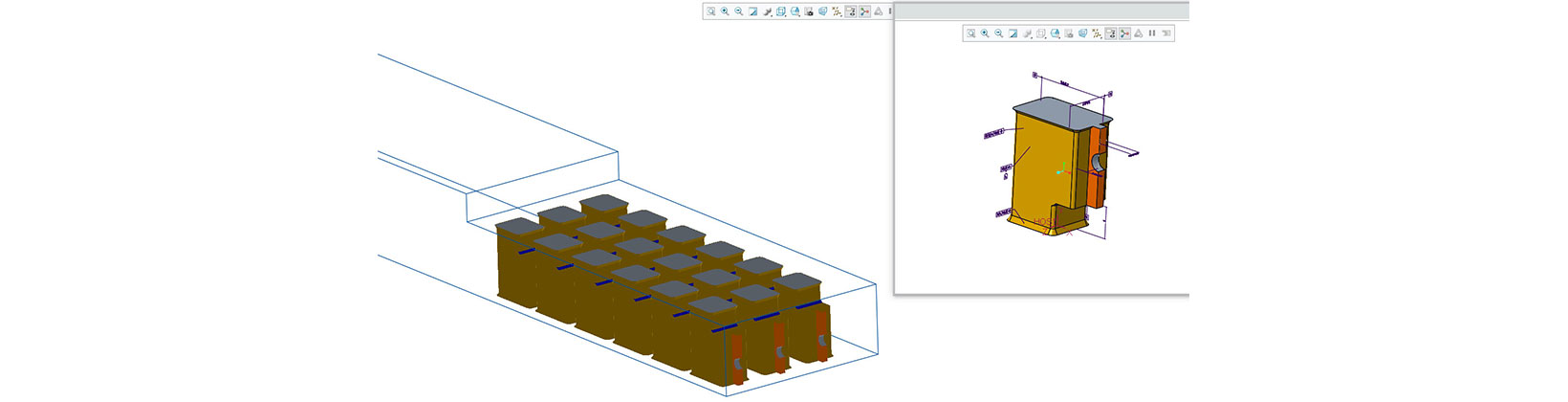
Challenge
These library components are intended to ensure flexibility in a defined manner (assembly constraints, dimensioning, and features) and classify them as standard usage (verified geometry definition). Any library components that do not adhere to this definition should be used as “custom.” Additionally, verification of the target geometry should be ensured.
Current Situation
Library parts have already been used within the company. However, it was not possible to directly use them from PDM-Link using Creo out-of-the-box functionalities. Since making direct changes to a part would also alter the released part, it was copied from Windchill locally, dimensions and features were adjusted, and then it was introduced through Creo’s built-in tools. Additionally, all annotation elements had to be transferred manually . Errors could easily occur, posing a risk to customer acceptance. Moreover, subsequent traceability to the original library part was no longer possible. Creo merge or inheritance feature could not be used here due to various missing functionalities in either case.
Solution
We proposed a toolkit application as the solution, which was divided into three areas:
Preparation:
- Multiple assembly constraints to facilitate easy placement in the target part.
- Dimensioning with rules that allow standardisation of dimensions for specific areas.
- Options to enable or disable defined features/features
groups and provide them to end users in a user-friendly selection interface.
Reuse:
Insertion of a custom application feature type that enables the assembly and manipulation of library parts through an interface.
Predefined annotation elements are also transferred to avoid potential sources of error.
Additionally, these features can be easily edited for future adjustments. Different revisions of library parts can be updated or replaced.
A notable feature is the ability to use different revisions within a single part or assembly.
Validation:
A validation mechanism is implemented to verify the created features based on their definition and surface geometry, classifying them as either “Standard” or “Custom”. This classification is provided using designated parameters for Windchill. For the user, the information is clearly displayed in a tree structure with color-coded highlighting in the Creo navigation area.
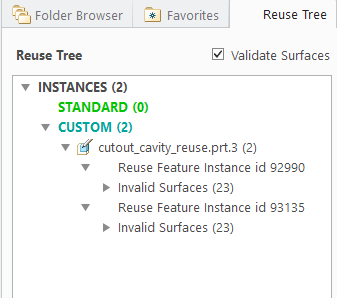
Benefit
The application developed in this project has resulted in a traceable and closed-loop process chain. It significantly simplifies the workflow for users and allows the identification and analysis of parts within Windchill. This, in turn, facilitates the creation of Technical Data Package (TDP) content and ensures that relevant documents can be collected and provided alongside the 3D model. Additionally, Windchill offers the capability to perform various analyses on standard and custom components, enabling evaluations for potential rule adjustments to library parts. This process promotes the normalization of custom reuse features and provides insights into possible modifications for the future.